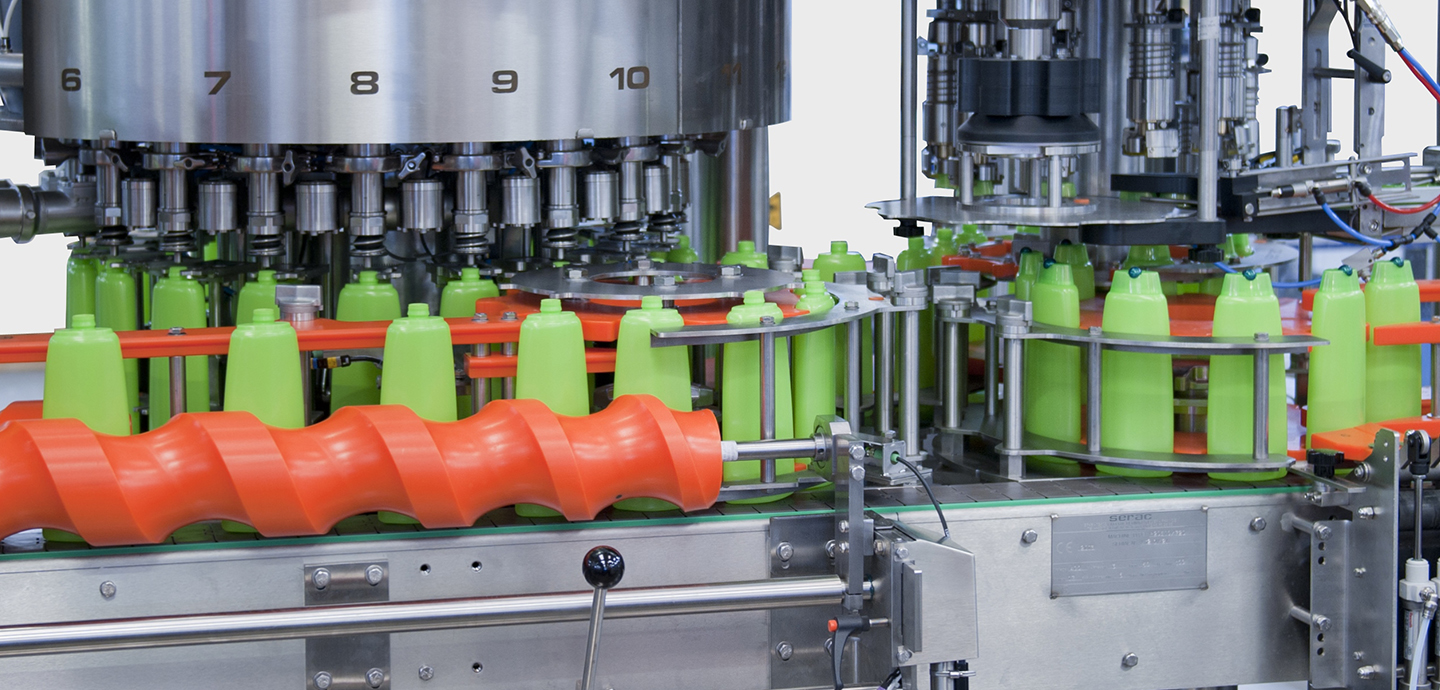
Optimize the process
Offering to manufacturers the possibility to use one single equipment for a large variety of products and packaging while saving on costs and maintaining their environmental footprint under control, rotary weight fillers are increasingly considered as the best technical option for process optimization on the hair care market.
“ More than ever, filling lines must be highly flexible, easy to operate and easy to clean in order to help manufacturers maintain the overall cost-efficiency of their packaging process. “
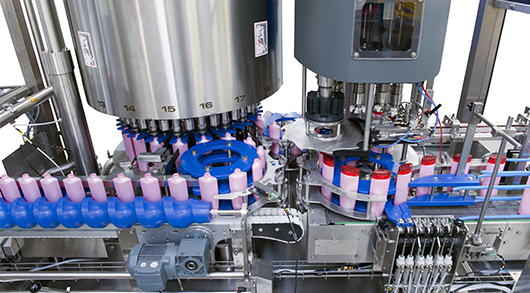
Firm handling of containers all along the filling and capping process
Versatile filling lines for varied products and packagings
Based on gravity or by a slight overpressure and using highly versatile filling nozzles, the Serac weigh filling technology is adapted for a wide range of products, from liquid to viscous, sticky or foaming ones. The use of a gravimetric tank, where the product load is maintained at a constant level, ensures a continuous and regular laminar flow without any pressure loss for a perfectly flat filling up to the bottle’s shoulder area.
Weight filling units are also highly versatile from a packaging point of view, since they can accommodate a 1 to 20 ratio which is much higher than for volumetric filling units.
The rotary weigh filling technology additionally offers the benefit of a positive handling of containers all along the packaging process. Instead of being moved in line on conveyors, each container is held during filling and between filling and capping operations. This allows to use the same equipment for all kinds of shapes (rounded, tapered, reversed, and asymmetrical) as well as to handle lighter and smaller containers with no risk of damage or product splash.
Finally, advanced rotary weigh filling lines can be equipped with state-of-the-art brushless capping units that are suitable for the many cap types and ensure a tight closure of the container thanks to torque modulation during screwing.
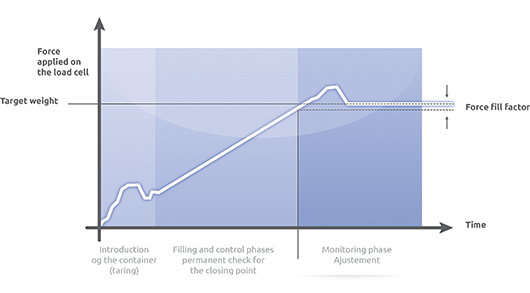
Weight filling is the only filling tecchnology that controls the amount of product as it sfills the bottle, not after?!
Product loss reduction through extremely accurate filling
Reducing the product loss of high-end products such as hair care products is one of the best ways to improve the cost-efficiency of a packaging line. Avoiding drops outside the bottle and product splashes due to harsh handling is the first step to which rotary weigh fillers contribute with ultra-clean nozzles that perfectly control the product cut-off and a positive handling of the containers all through the filling process.
However, far bigger savings will be generated by ensuring a perfectly accurate quantity of product inside containers. Accurate filling avoids rejection of under-filled containers and product giveaways in overfilled ones. Such savings can easily compensate for the cost of a filling machine within a few years of operation. Also as far as accuracy is concerned, weigh filling is much more reliable than any other technology.
Firstly, weigh filling is the only technology that controls the weight of product inside the container after it has gone through the nozzles, that is to say the conformity with the nominal quantity printed on the packaging. This is why weigh fillers can be used in legal metrology, as long as that they have obtained an ? Automatic Weighing Instrument ? (AWI) type approval certificate, whereas volumetric or flow metering systems cannot. The permanent weight control allows to detect any filling defect and to adjust immediately the filling parameters of each nozzle.
Secondly, unlike volumetric systems, weigh filling is unaffected by volume variation caused by temperature changes. This avoids manual adjustments of the machine’s settings, which are subject to human error.
Thirdly, weigh fillers do not generate any product aeration. Product aeration, which is created in volumetric systems by the use of piston/cylinder assemblies, is uneven and keeps varying. It thus often imposes an overfilling of containers in order to offset deviations in product quantity. Such giveaways can be totally avoided with weigh fillers.
Optimized running and changeovers for maximum availability of the line
As mentioned above, the natural flexibility offered by the weigh filling technology reduces the number of tooling changeovers. However, when needed, these changeovers are fast and easy. They are based on lightweight colour coded pieces with blockers, a plug-and-play system that prevents wrong pieces to be used, even from non-trained operators. The system requires no further fine-tuning of the machine’s settings, which saves both time and product.
The specific design of weigh fillers, which involves neither piston nor gasket, also allows significant time savings on flushing and cleaning operations. Those are crucial to ensure the availability and cost-efficiency of the line when various products are to be packed on the same machine. A special vacuum pump can even be added on the equipment to further reduce the flushing time and thus the global downtime of the line.
Rotary weigh fillers can finally be coupled with a wide variety of other machines thanks to integration concepts such as the Superblock proposed by Serac, which offer the benefit of creating fully synchronized machines (unscrambler, labeller, case-packer) for higher performance and easier operation.
Cleaning effluents under control
Producing smaller batches of varied products implies more cleaning cycles which can increase the environmental impact of a production site. This is why, besides being flexible, filling lines must also be very easy to clean, with a minimum use of water.
Looking in detail at a typical weigh filling unit proposed by Serac, one can see that the whole product circuit is designed with easy cleaning in mind. It involves no joint or gasket that are hard to clean and subject to wear, and no mechanical part or dynamic seal in direct contact with the product. The cleaning time is thus reduced, especially with efficient CIP equipment. Those proposed by Serac are designed to remove all product traces with minimal use of cleaning solution, both inside and outside of the tank. They work in closed sanitation circuit and make use of multidirectional sanitary spray balls for a higher impact of liquid jets, as well as of a cleaning manifold for a bigger flow of cleaning solution through the nozzles. Tanks are 100% self-draining and convex shaped with no dead corners where product could be retained.
上一篇:Packaging machines suited to the household cleaning products and personal care markets
下一篇:Sauces: 3 product trends that reveal the benefits of weight filling