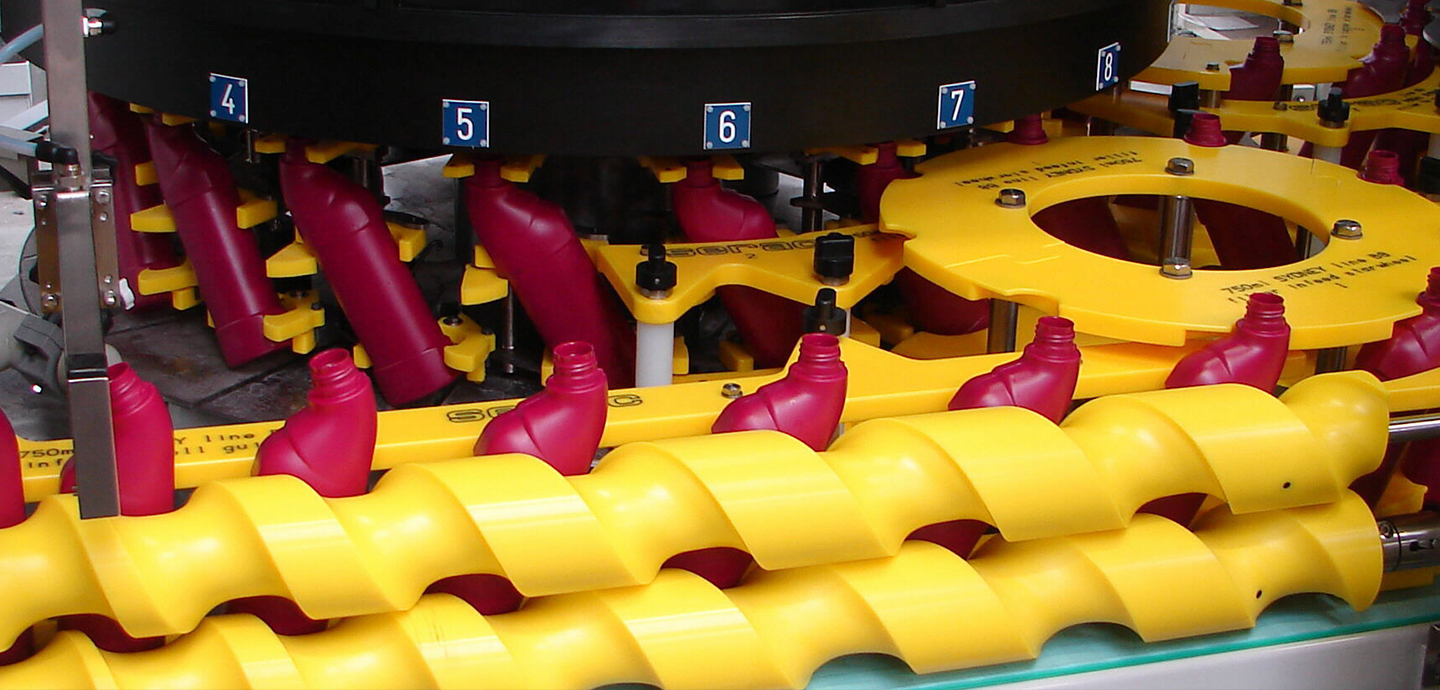
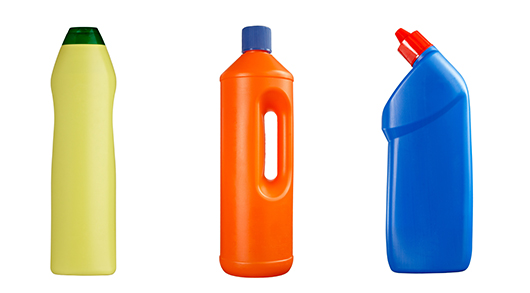
New packaging combine safety and ease of use
Corrosive formulas are unlikely to vanish soon
Despite different evolutions on mature and emerging?markets, sales of household cleaning products are still?growing at reasonable pace on a worldwide scale.
Although environmental concern might affect the?sales of some specific products in favor of ? natural ??cleaning agents, the efficiency benefit remains on?the side of more corrosive formulas which will still be?around for a long time.
Among this corrosive products, bleach is the one that?probably has the most promising future: first, it can?enter a majority of households in countries where?hygiene level is still under development and where?consumers look for cleaning and sanitization functions?at an affordable cost; second, it meets the expectations??of households affected by a loss of purchasing power?by offering a multi-functional solution that favorably?replaces different task-specific cleaning products.
For all these reasons, the future of corrosive household?cleaning products seems not blurred enough to stop?considering their manufacturing on the long term.
“ When properly designed and built to withstand contact with corrosive products, a filling machine can generate yearly maintenance costs that represent less than 1% of the acquisition cost. “
Acquisition cost has to be balanced with TCO and OEE
Aggressive products can significantly reduce machine’s?lifetime if they are not designed to be corrosion-proof.?Spilled liquids can seep in the machine body and spread?corrosion across components, thus generating high?maintenance costs and machine downtime.
When properly designed and built to withstand contact?with corrosive products, a filling machine can generate?yearly maintenance costs that represent less than?1% of the acquisition cost. With less breakdowns and?maintenance operations, the overall availability of the?machine is obviously higher and production can be?conducted without trouble over a longer period.
Corrosion-proof design not only means to use chemical?resistant materials for sensitive parts. Higher?robustness must be sought after for all components,?through specific materials, coatings, and protection?methods (such as overpressure for electrical parts
and mechanical drives). Minimizing the number of?welds in the machine design also contributes to?extend its lifetime.
Proactive protection of the equipment is essential as well?since it avoids repeated contact with corrosive products?where not intended. Proactive protection is obtained?through a clean production environment (less drips, for?example), full mastery of corrosive fumes, operational?reliability and high cleanability.
Operators’ safety is essential as well
Machines that are specifically designed for?corrosive products can include a whole array of?options to secure that operators are not exposed?to harmful substances.
Serac’s RC filling machine range offers for example a?totally closed and tight cabinet equipped with proven?extraction mechanisms to avoid the propagation of?vapors, and an automatic cut-off system connected with?doors opening.
Customized design better suits specific product requirements Corrosion depends
Corrosion depends on several parameters, such as?chemical composition, temperature, abrasiveness,?pressure or fluid velocity, which can vary significantly?from one product to another.
Since various corrosion-proof materials can be used?in the building of the filling machine, and no single?combination proves ideal for every product, design?should always be carried out in close partnership with?the end-user. With his own parameters in mind, he will?be able to guide the machine manufacturer towards?the proper choice of materials for the environment?considered and thus benefit from the longest possible?lifetime for his machine.
Corrosion-proof materials used by Serac in its RC?filling machines include polyethylene or polypropylene,?316L stainless steel, titanium and even Hastelloy.
Serac also proposes Halar coated stainless steel?tanks that offer higher resistance to mechanical?stresses, chemicals and temperature. Such tanks are?particularly suited for highly viscous products that?require overpressure and applications dealing with?hot fluids or hot cleaning agents.
As we can see, from ROI point of view, several arguments?plead in favor of machines specifically designed to?withstand corrosion over a long operational lifetime.?However, to win the final decision, such machines still?have to be flexible enough to make sure they will be?able to adapt market evolutions over the long term.
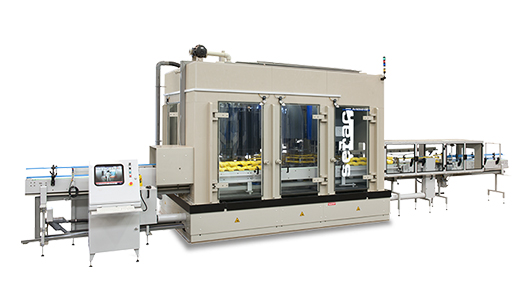
Filler-capper made of corrosion resistant materials
The RC filler
With undisputed experience gained through its?long term collaboration with HPC industry leaders,?and mastery over all kinds of packagings (angle?or straight necks, complex caps…) and formulas?(concentrated, scented…), Serac positions itself as?a reliable partner for developing machines with a?long-term business overview.?When designing its RC filling machine range, Serac?has also emphasized flexibility by using the Plug-On??technology for format changes. Plug-on change tools?enable the production of multiple formats on the same?machine, with quick dismantling and assembling.?Combining profitability with market adaptation,?Serac’s RC filling machines definitely offer all the?benefits required for investing in a long-lasting?production equipment.